How India’s first semiconductor fabrication plant can help plug into the global value chain
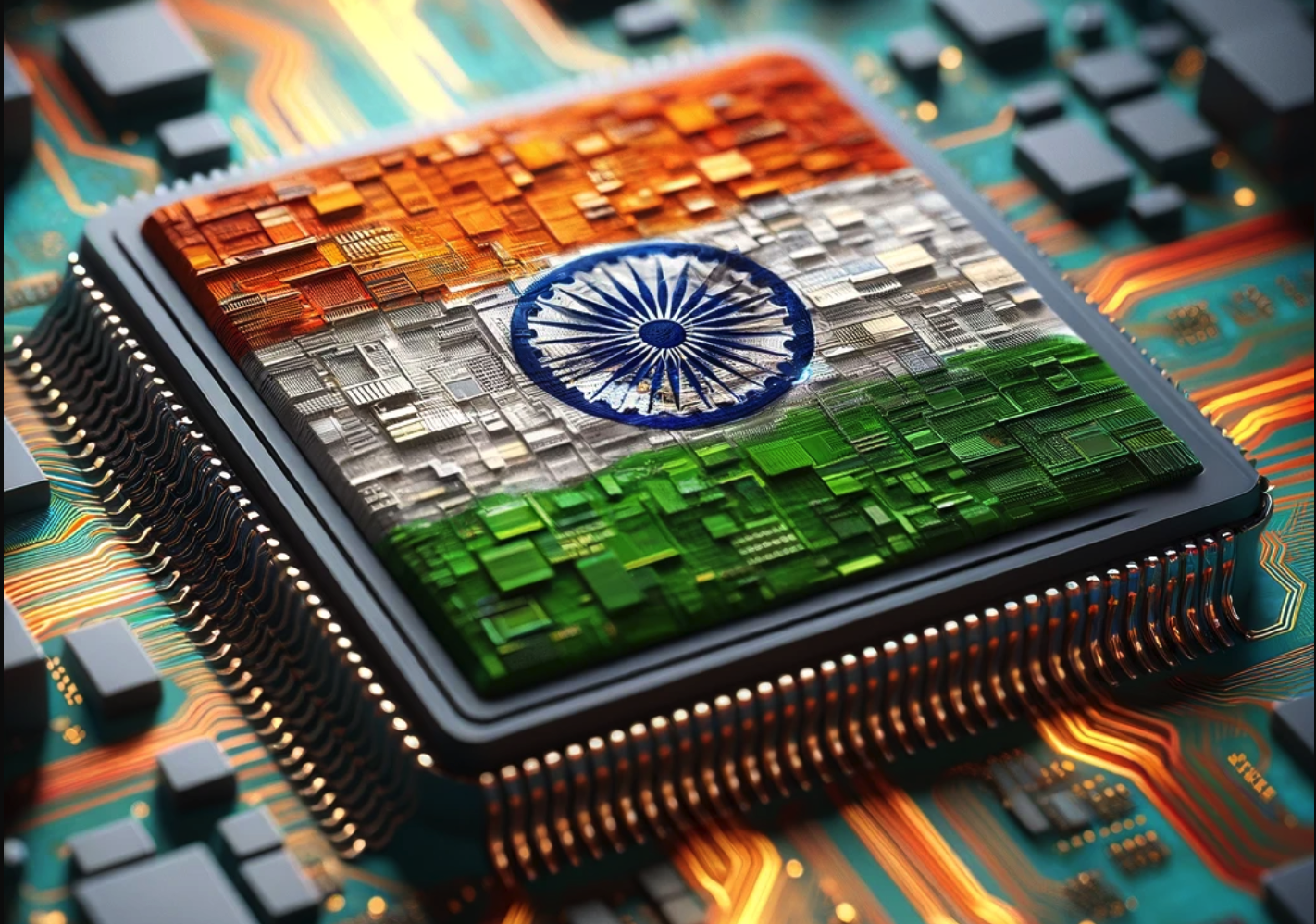
- 02 Mar 2024
Why is it in the News?
The Union Cabinet recently approved the country's first semiconductor fab to be made by the Tata Group in collaboration with Powerchip Taiwan.
What is Semiconductor Fabrication?
- The semiconductor fabrication process is a complex and highly specialized series of steps that transform raw materials into functional electronic components.
- This process involves a multitude of techniques and technologies, with each stage requiring precise control and attention to detail.
- A semiconductor fab -- short for fabrication -- is a manufacturing plant in which raw silicon wafers are turned into integrated circuits (ICs).
- A fab lab features a clean room where ICs are etched onto wafers.
- The completed chips are sent to a back-end assembly and test facility before they are packaged and sold.
- A semiconductor fab facility always includes a clean room -- so known because its environment is carefully controlled to eliminate dust and vibrations and to keep the temperature and humidity within a specific narrow range.
- Contamination can enter the fab environment through external sources, resulting in damage to products that can affect overall yield.
- To minimize the losses, all potential sources of contamination are thoroughly analysed and cleaned.
- For example, the tools used in the chip manufacturing process have low levels of particulates and fibres.
- The goal is to ensure that extraneous contamination is not introduced into the semiconductor fab to ensure the highest quality of the final products.
Technology Used in Semiconductor Fab Labs:
- Photolithography: Photolithography is a crucial optical process in the fabrication process, as it is used to create intricate circuit patterns on a single wafer's surface.
- This is achieved by coating the wafer with a photosensitive material, called a photoresist, and then exposing it to high-wavelength deep ultraviolet (DUV) or extreme ultraviolet (EUV) light through a mask containing the desired pattern.
- The exposed photoresist undergoes a chemical change, which allows it to be selectively removed.
- It leaves behind a patterned layer that serves as a protective layer for subsequent processing steps, such as etching and deposition.