PS4 Engine
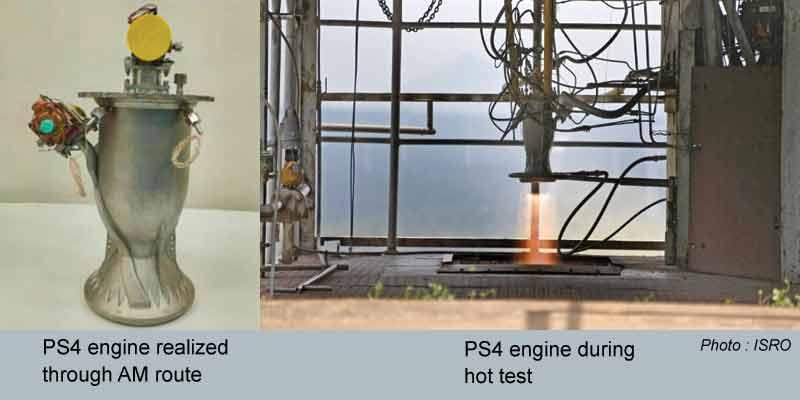
- 11 May 2024
Why is it in the News?
Recently, the Indian Space Research Organisation (ISRO) successfully tested a liquid rocket engine made with the help of additive manufacturing technology — commonly known as 3D printing.
About PS4 Engine:
- ISRO has successfully conducted a long-duration test of its PS4 engine, re-designed for production using cutting-edge additive manufacturing (AM) techniques, also known in common parlance as 3D printing, and crafted in the Indian industry.
- The PS4 engine is the uppermost stage of the Polar Satellite Launch Vehicle (PSLV), comprising two Earth-storable liquid engines.
- The engine uses the earth-storable bipropellant combinations of Nitrogen Tetroxide as oxidiser and Mono Methyl Hydrazine as fuel in pressure-fed mode.
- It was developed by ISRO's Liquid Propulsion Systems Centre (LPSC).
- LPSC redesigned the engine making it amenable to the Design for Additive Manufacturing (DfAM) concept thereby gaining considerable advantages.
- It was developed by ISRO's Liquid Propulsion Systems Centre (LPSC).
- The manufacturing of the engine was done by the Indian industry partner, Wipro 3D, and the engine was hot tested at ISRO Propulsion Complex, Mahendragiri, Tamil Nadu.
Why did ISRO use 3D printing to build the PS4 engine?
- The technology helped ISRO bring down the number of parts in the engine from 14 to a single piece.
- The space agency was able to eliminate 19 weld joints and saved 97% of the raw material.
- It also reduced the overall production time by 60%.
What is 3D Printing?
- 3D printing is a process that uses computer-created design to make three-dimensional objects layer by layer.
- It is an additive process, in which layers of a material like plastic, composites or bio-materials are built up to construct objects that range in shape, size, rigidity, and colour.
How is 3D printing done?
- To carry out 3D printing, one needs a personal computer connected to a 3D printer.
- All they need to do is design a 3D model of the required object on computer-aid design (CAD) software and press ‘print’.
- The 3D printer does the rest of the job.
- 3D printers construct the desired object by using a layering method, which is the complete opposite of the subtractive manufacturing processes.
- The (3D) printers act generally the same as a traditional inkjet printer in the direct 3D printing process, where a nozzle moves back and forth while dispensing a wax or plastic-like polymer layer-by-layer, waiting for that layer to dry, then adding the next level.
- It essentially adds hundreds or thousands of 2D prints on top of one another to make a three-dimensional object.
- Notably, these machines are capable of printing anything from ordinary objects like a ball or a spoon to complex moving parts like hinges and wheels.
- We can print a whole bike, handlebars, saddle, frame, wheels, brakes, pedals and chain–ready assembled, without using any tools.
- It’s just a question of leaving gaps in the right places.
3D Printing (The Hindu)
- 19 Aug 2023
What is the News ?
India’s first 3D printed Post Office was inaugurated in Bengaluru’s Cambridge Layout.
Facts About:
- India’s pioneering 3D-printed post office located in Bengaluru’s Cambridge Layout was recently inaugurated.
3D Printed Post Office
- Swift Build: The 3D-printed post office was constructed in just 43 days, surpassing the original deadline by two days.
- Construction Team: Larsen & Toubro Limited undertook the project in collaboration with IIT Madras.
Technological Process
- Spatial Dimension: The post office covers an area of 1,021 square feet and was created using advanced 3D concrete printing.
- Automated Procedure: Robotic printers used an automated process to layer concrete according to the approved design.
- Strong Bonding: A specially formulated quick-hardening concrete ensured strong bonding between layers.
- Rapid Construction: With robotic precision and pre-embedded designs, the project was completed in just 43 days, far shorter than the conventional 6 to 8 months.
Advantages of 3D Printing
- Cost-Effective: The project cost ?23 lakhs, indicating a 30-40% cost reduction compared to traditional methods.
- Showcasing Technology: The project highlighted concrete 3D printing technology using indigenous machinery and robots, showcasing its scalability.
Distinctive Features
- Continuous Perimeter: The project boasted continuous perimeter construction without vertical joints.
- Flexibility: The 3D printing accommodated curved surfaces and different site dimensions, overcoming flat wall limitations.
- Structural Innovation: Continuous reinforced concrete footing and three-layer walls were created, enhancing structural integrity.
- Reduced Timeline: The innovative technique drastically reduced the construction timeline to 43 days, minimizing material wastage.
Source: https://www.google.co.in/url?sa=t&rct=j&q=&esrc=s&source=web&cd=&ved=2ahUKEwi88OSW3aGBAxVDTWwGHafnBzMQFnoECB8QAQ&url=https%3A%2F%2Fwww.thehindu.com%2Fnews%2Fcities%2Fbangalore%2Findia-first-3d-printed-post-office-is-now-open-for-business-in-bengaluru%2Farticle67208897.ece&usg=AOvVaw1xcvOgM9Z66xFGFeSZ-7W_&opi=89978449